Silicone A-100(Clear Base)
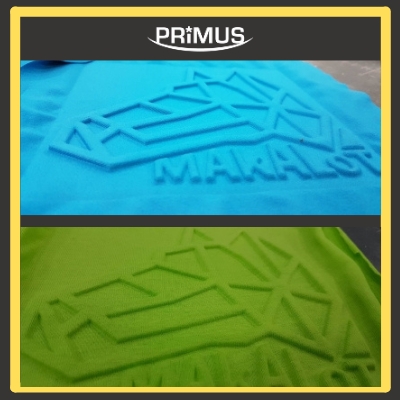
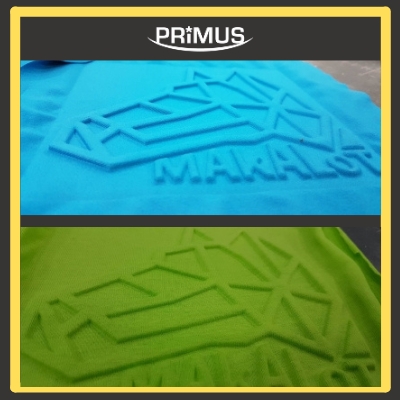
Technical Data Sheet
(Silicone A-100/A-100W/Base-KS and Silicone B-10 Catalyst)
(Silicone A-100/A-100W/Base-KS and Silicone B-10 Catalyst)
Details:
It is a silicone ink developed specially for screen printing inks on garment textile field, with two components system. Silicone A-100/A-100W is Clear/White Base and Silicone B-10 is a catalyst to be added 10% by weight of the Silicone Base. They are entirely eco-friendly products that do not contain Heavy Metals, Azo, PVC, Phthalates, Organo-tin, and Formaldehyde. Silicone Base-KS is a silver base with high opacity property especially for dark fabric.
Specialty:
- Multi colors printable, very soft hand
- High glossy effect
- Suitable for high elastic fabrics
- Suitable for emboss molding process
- No harmful or distracting odors in the work place.
Guidance:
- To build up pattern thickness, the printing in each layer must be dried to touch before applying next print. The more printing time applied, the higher thickness achieved.
- Item Info:
1) Silicone A-100(Clear Base) - 2) Silicone A-100W(White Base)
3) Silicone Base-KS(High opaque silver base for dark fabric)
4) Silicone B-10 (Catalyst, 2 hours pot life after mixing with base)
5) Reducer C-250 (Adjust printing paste viscosity)
6) Silicone Pigments (12 colors available)
Recommend Dosage: 10-15% by weight of Silicone A-100/A-100W/Base-KS - Avoid wet on wet printing application.
- When bubbles appear on surface, please keep it idled till it flows evenly on surface or blow cold air on it to bubble out.
- To create certain coverage on dark ground, Silicone Base-KS is quick flash dry for under coat before applying silicone colors on top.
- Recommended recipes for EMBOSS Molding:
1. Mixing A-100 and B-10 as a print solution.
2. Coating direct on garment, mesh count 39T/CM(100T/IN), screen printing enough ink deposit is important.
3. Place taffeta or fabric on the coated area, then directly go Molding process at 180C x 20 seconds.
Precautions:
Printing Parameters:
- Keep the screen in the flooded position while print stops. Or, go for screen wash during a temporary stop.
- Containers must maintain air-tight seal while not in use.
- During production, heat application can be applied to speed up the process. Failure to cure ink at recommended time and temperature may result in poor wash fastness.
- It is recommended to add enough printing inks (with Fixer B-10) to be able to print within Fixing Agent’s Pot Life to avoid spoiled.
- Any application not referred in this product information should be pre-tested or consulted with Primus Technical Service prior to print.
Printing Parameters:
1100% Polyester, Blended or High elastic fabrics | Flash: 130℃(266℉) x 10-15 seconds Cure: 120℃(248℉) ×2 minutes |
||
Durometer: 60-70 Edge: Sharp |
100-180 t/in (39-71 t/cm) | ||
Silicone B-10 (Pot Life: 2 Hour) Reducer C-250 |
18-40℃(65-90℉) Use within one year of receipt. Avoid exposing under direct sunlight. Keep drums sealed tight at all times. |
||
Additive Screen Cleaner P3 | Available upon request (MSDS) |